Air Cargo Lifts Handle Large Containers
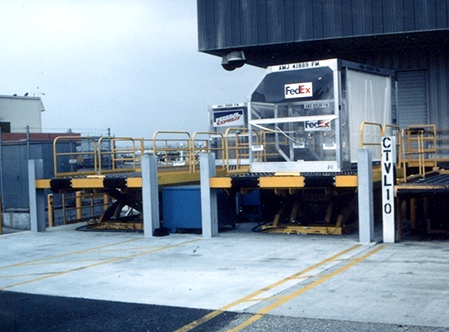
Introduction
Air Cargo lifts help transfer heavy cargo containers between variable truck bed heights and fixed dock.
Project Challenge
As one of the world’s largest shipping/logistics companies, FedEx required a lifting solution that could safely and efficiently transfer air cargo containers of various sizes between ground level and dock elevation at its distribution centers and terminals. In finding the right solution, Autoquip faced multiple challenges, including strict performance criterion that would provide uninterrupted and reliable service, and a useful life of 10 years or more under extremely rigorous operating conditions.
Several of the design challenges associated with this dock lift application:
- Must lift/transfer containers weighing up to 15,000 lbs with minimal deflection.
- Containers sizes vary, up to 12 ft x 12 ft 3. Must be able to manually transfer containers between trucks and building.
- Manual stops and locks must be utilized to prevent unintentional container movement.
- Redundant systems must be in place in lieu of motor failures or electrical outages.
- Must be able to withstand severe/outdoor-operating conditions.
Our Solution
Autoquip recommended a custom-engineered Tork – T1 scissor lift designed and rated to lift the 50,000 pound requirement of each turbine engine. Several design features were added to the Tork scissor lift so that risk of damaging the turbine casings or stressing the parts while it is laid on its side would be minimized. These design features will stabilize the turbine engine while the overhaul takes place.
Design Features:
- The Tork scissor lift is designed to set on guide rails to create stable flooring as the lift moves along 358” to the power station. This also creates a portable solution for moving the rails and lift to all four power generation stations.
- Custom fixtures built on top of the lift platform to cradle the turbine engine and insure a safe transfer.
- The platform also shuttles and extends to help align the gas turbines closer to the power generators.
- Two vertical cylinders are used for the required stroke which will raise the lift only 8”.
- The vertical cylinders are designed with rod locks and are activated any time the lift is stopped which locks the lift in place and prevents any drifting.
- Pressure transducers sense and alert the operator if they have put more weight on the lift than the rated capacity.
The Results
The design team at Autoquip utilized an American Lift Scissor design to effectively meet all the performance requirements of this severe duty application. In order to handle the extremely large, extremely heavy loads with minimal deflection, a heavy-duty Scissor leg assembly was designed utilizing large, structural steel tubing leg material, captured scissor rollers, and a one-piece axle pin. The large platforms required for this application were designed to optimize operator safety, as well as product stability.
Platforms are equipped with a non-skid walkway, roller conveyor deck, OSHA-compliant personnel guardrails, and manually operated pallet stops. Other premium lift features providing durability and longevity include self-aligning hydraulic cylinders, high-impact self-lubricated bushings, and structural steel cross-members at every pinned joint, and low-pressure hydraulic circuit.
Basic Equipment Specifications:
Lift Model: 49AC150-13
Lifting Capacity: 15,000 lbs.
Platform Size: 156″ x 156″ with non-skid walking surface, roller transfer deck, manual pallet stops, and OSHA-compliant guard rails
Vertical Travel: 49″
Lifting Speed: 7 FPM
Redundancies: redundant hydraulic power unit; manual override “Down” valve